2020年,特斯拉正式提出4680大圓柱電池技術,通過無極耳(也稱全極耳)技術,創新地解決了圓柱電池體積增大后內阻和發熱量問題,滿足高能量密度、高功率等性能要求,使得大圓柱正式進入行業視野。
大圓柱電池采用鋼殼設計,對極致化學體系兼容性好,且制造成本低、易于標準化,越來越受到中高端乘用車市場的青睞,大部分車企都將大圓柱電池作為主要路線之一。
值得注意的是,無極耳電池技術雖然解決了圓柱電池電流路徑的問題,但正負極異側設計所帶來的電子傳輸路徑仍然過長,導致內阻偏大,且受限于傳統材料和工藝設計,無法滿足高端乘用車應用市場的極致需求。
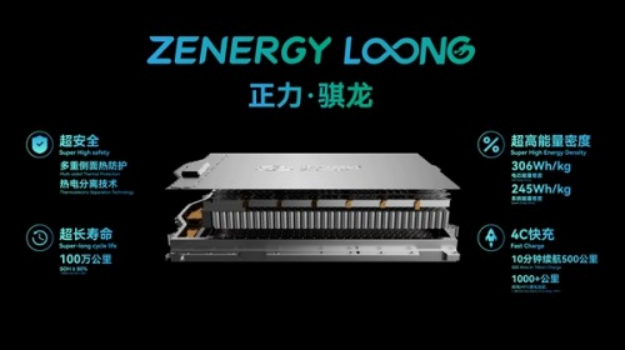
近日,國內電池企業在大圓柱技術創新上已先行一步,基于結構和材料層面變革性的創新,引領大圓柱技術新趨勢。4月19日,正力新能發布全球首款雙重半固態大圓柱電池——“正力·騏龍”大圓柱電池系統,該電池采用正力新能獨創的“極能環、極能蓋、極能態”三大核心技術,集超安全、超高能量密度、及整車100萬公里超長壽命和充電10分鐘續航500公里的超快充技術于一體,支持純電MPV車型,滿電續航1000公里以上,且電池包容量高達170kWh,是目前國內乘用車電池中帶電量最大的電池系統。
破解行業痛點,正力新能獨創三大極能電芯技術 數據顯示,今年一季度中國市場新能源汽車銷量達到209萬輛,新車滲透率超過30%,隨著新能源汽車的普及,高端乘用車需求越來越大,主流車企陸續推出高端車型來吸引消費者;同時,寶馬、大眾、奔馳等海外車企也在加碼高端乘用車布局。
現階段,受限于電池材料、設計和工藝難題,主流電池仍無法滿足高端乘用車對續航、充電速度、安全和使用壽命的極致需求。正力新能基于LISA3-2-1研發戰略,針對高端乘用車市場需求痛點,依托正力極能技術電芯體系,推出46系列大圓柱電池,電芯單體容量達到49.5Ah。
據正力新能介紹,該大圓柱電芯是公司基于材料、結構、設計和工藝裝備等維度創新,并通過“極能環、極能蓋和極能態”三大創新形態產出的成果。
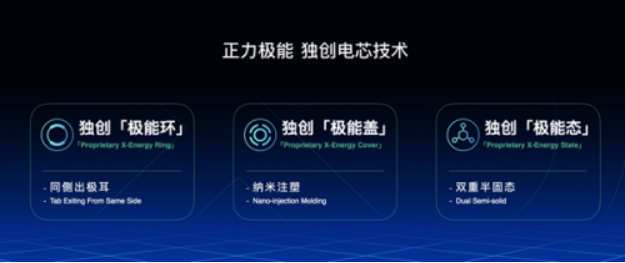
極能環技術:傳統4680圓柱電芯正負極采用異側設計,電子傳輸路徑過長,內阻偏大。正力新能獨創同側出極耳技術,大幅縮短電子傳輸路徑,降低歐姆電阻。據悉,為了實現同側出極耳結構,正力新能開發了激光模切卷繞一體化的閉環圓柱制造設備,解決了同側出極耳的工藝難題,實現了產品的全面升級。相較于無極耳技術,極能環技術大圓柱電芯電子路徑縮短80%、歐姆阻抗下降30%,體積利用率提升3%。
極能蓋技術:正力新能將傳統的氟橡膠密封圈設計升級為刻蝕納米注塑技術,相較于傳統的頂蓋集成技術,該技術可降低10%成本;PPS與頂蓋、極柱表面形成納米級的錨栓結構和化學鍵結合,氦檢氣密性提升兩個數量級,是傳統密封圈水平的100倍,從而提高了電芯單體空間利用率及全生命周期可靠性。
極能態技術:即雙重半固態電芯技術:超高鎳正極材料的固態電解質表面修飾技術、固態電解質復合隔膜。得益于雙重半固態技術的加持,大圓柱電芯的熱穩定性得到明顯改善,失效起始溫度提高10度,失效后最高溫度降低150°C。此外,在安全性得到提升的同時,電芯的功率性能也得到了改善,零下20°C低溫功率提升了20%。
可以看到,基于大圓柱對極致化學體系的良好兼容性,以及公司對電池材料技術的創新研發,正力新能在材料創新上,正極使用超高鎳,負極使用硅碳,同時率先在行業應用固態電解質表面修飾技術、固態電解質復合隔膜技術,使得公司的46圓柱電芯,能量密度達到306Wh/kg,處于行業領先水平。
在結構和設計創新上,正力新能獨創了同側出極耳電芯技術,解決了現有4680圓柱電芯內阻偏大的問題,同時首創了納米注塑技術不僅提高了電芯單體空間利用率及全生命周期可靠性,還降低了電芯成本。
基于材料、結構方面的開創性創新能力,正力新能也同步進行了相關技術布局。截至目前,正力極能電芯技術已經布局291項專利,其中納米注塑25項、高鎳+硅碳64項、半固態技術16項、圓柱電芯技術125項、圓柱電池包技術61項。
170kWh引領超長續航正力·騏龍全新定義“三超一快” 與目前業界在大圓柱電池技術上多采用跟隨狀態不同,正力新能率先開創同側出極耳、納米注塑、雙重半固態技術,破解了當前大圓柱電芯的行業痛點,進一步探索了大圓柱電池的性能、安全、成本極限,以能量密度306Wh/kg,單顆電芯容量49.5Ah,4C超快充性能等多個優異性能,滿足高端乘用車的極致需求。
依托三大獨創技術,基于正力新能46系列圓柱電芯,正力新能推出的“正力·騏龍”大圓柱電池產品,帶電量達到170kWh,創下目前國內新能源乘用車電池包容量之最。不過,電池容量只是正力新能在系統層面創新的一個縮影,“正力·騏龍”在安全、壽命、快充、CTC結構設計等方面的創新也可圈可點。
安全層面,現階段如何保障超高電量產品的安全性是大容量產品的“珠穆朗瑪”。除了采用極致安全的46大尺寸圓柱電芯,正力新能在系統層面還進行了多重安全設計:
首先是應用熱電分離技術:電芯失效時防爆閥向下噴發排氣,保證乘員艙的安全,且與電氣連接區域上下隔離,防止拉弧二次短路,且仍能保證監控系統正常工作;
其次,應用多重側面熱防護技術,實現電池包級別的永不熱擴散(NTP)。
系統能量層面,以306Wh/kg超高能量密度的圓柱電芯為基礎,正力新能在系統結構上利用電池包上蓋與整車底盤集成的CTC設計,整包電量高達170kWh,是目前國內乘用車最大電量電池系統。
為延長電池系統循環壽命,正力·騏龍采用系統高效均衡熱管理,保證電池工作環境的一致性;多支路并聯設計,各支路流量偏差<3%;熱阻均衡逆向設計,快充工況下整包電芯溫差小于5℃,從而保障整車全生命周期內可以實現100萬公里的超長續航。
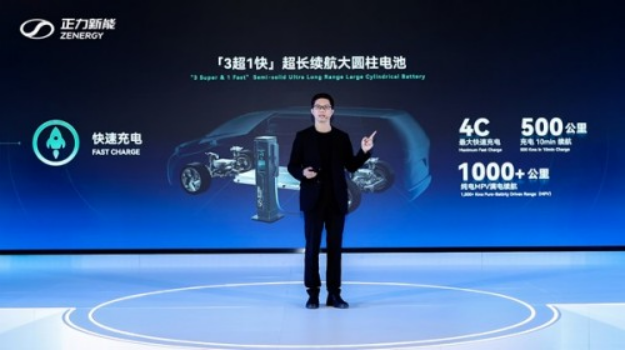
在快充方面,正力·騏龍采用800V高壓快充平臺電氣設計和系統超強熱管理。其中,800V平臺電氣設計,滿足高壓大電流快充;高效熱管理,快充最大溫升小于30°C;同時集成BDU液冷,保證電氣件的工作穩定性;正力騏龍可以支持4C快速充電,充電10分鐘續航500公里。實現純電MPV車型滿電續航1000公里以上,真正做到,千里奔赴,一充即達;
憑借170kWh的超大容量、NTP的超安全保障、245Wh/kg的超高系統能量密度、100萬公里的超長壽命,以及4C的超快充性能,正力新能正重新定義“三超一快”,以極致性能引領高端乘用車電池技術新趨勢。
“正力·騏龍”電池系統也已于2023年完成裝機測試,并且已由整車廠送檢第三方權威檢測機構,電芯及電池包獲得了多項檢測認證證書。未來,隨著“正力·騏龍”電池以極致性能和體驗,陸續配套更多高端車型,必將不斷提升正力新能在全球電池市場的競爭力。
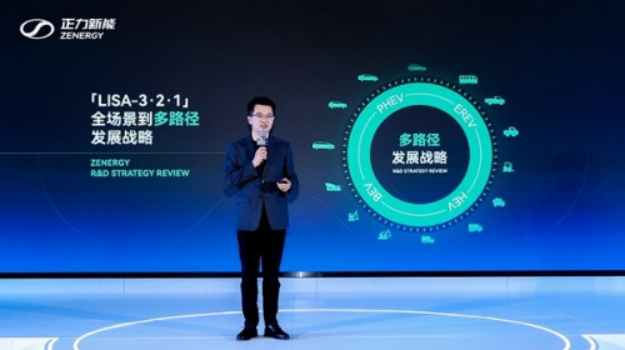
據悉,2023年,正力新能正式對外發布了「LISA-321」的長期研發技術戰略,并布局覆蓋「陸海空」全生態全應用場景的產品研發體系。在此基礎上,正力新能不斷實踐電化學材料差異化的探索,提供標準化電芯的解決方案,助力車企實現電池包平臺化,踐行多路徑均衡發展的長期戰略。
目前,正力新能已構建涵蓋BEV、PHEV、EREV和HEV等汽車,儲能、電動載人飛行器、電動船舶等全場景、多路徑的技術路線和產品矩陣,并在海陸空各領域都已經與全球客戶進行深度全面合作。